Introduction to Tubular Heaters
Tubular heaters represent a critical component in the field of industrial and commercial heating solutions. Known for their versatility and efficiency, tubular heaters are fundamentally electric heaters comprised of a tube-shaped structure that encloses a heating element. This design not only ensures robustness but also simplifies the installation and maintenance processes. The simplicity of their construction is one of the key reasons why tubular heaters are widely preferred compared to other heating alternatives.

In essence, a tubular heater consists of a metal sheath that houses a resistant wire, embedded in a compacted filler material such as magnesium oxide. The precise construction allows for the optimal transfer of heat from the resistant wire to the external environment while safeguarding the heating element from environmental damage and electrical shocks. The robust design guarantees durability and reliability, which is essential for various industrial applications.
An integral advantage of tubular heaters is their adaptability. They are employed in a myriad of settings, ranging from household appliances to industrial machinery, owing to their customizable shapes and mounting options. From straight to coiled, and finned to flanged configurations, tubular heaters can be tailored to fit the specific needs of diverse applications, ensuring efficient heat delivery regardless of the installation environment.
The efficiency of tubular heaters is noteworthy. These heaters are designed to convert a significant percentage of energy into heat with minimal losses, which is a paramount consideration in both energy conservation and operational cost reduction. Furthermore, tubular heaters provide uniform heat distribution, ensuring consistent performance and enhancing the overall process or operational efficiency.
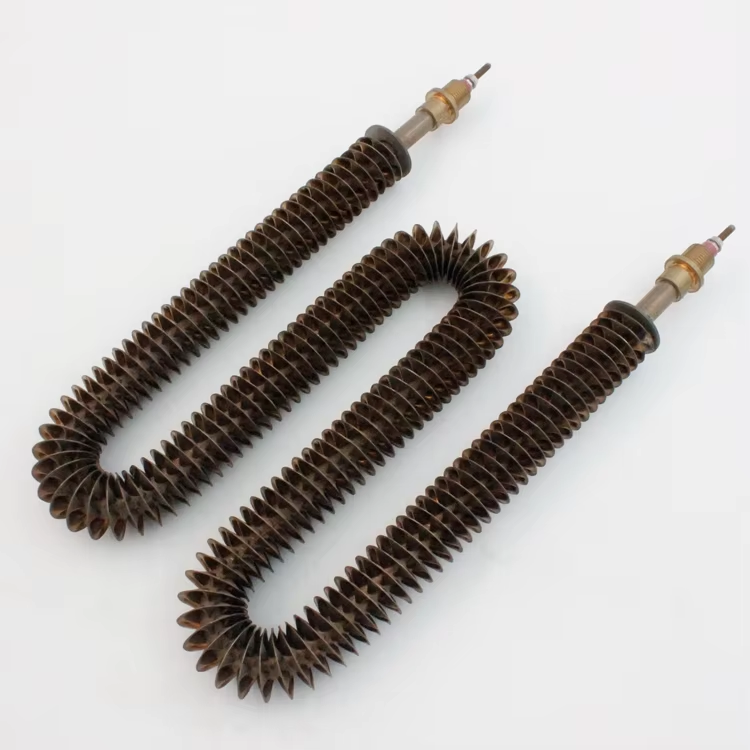
Reliability and longevity further set tubular heaters apart from other types of heaters. Their ability to withstand extreme temperatures, mechanical shocks, and corrosive environments makes them a preferred choice in industries where consistent performance and minimal downtimes are essential. Therefore, understanding the fundamental characteristics and advantages of tubular heaters illuminates their indispensable role in modern heating solutions.
Applications of Tubular Heaters
Tubular heaters, known for their versatility and efficiency, play a pivotal role in numerous industries and processes. They are prized for their ability to provide even, controlled heating, making them indispensable to a variety of applications. Below, we explore key sectors where these heaters are extensively utilized, highlighting real-world applications for manufacturing, food processing, and industrial heating systems.
In manufacturing, tubular heaters are critical in processes requiring precise temperature control. For example, in the plastics industry, they are employed in injection molding machines to maintain the ideal viscosity of plastics during melting and shaping. Similarly, in the metalworking sector, these heaters are used in annealing and heat treatment processes to alter the physical and sometimes chemical properties of metals, ensuring the desired strength and durability. The adaptability of tubular heaters allows them to be configured in various shapes and lengths, making them suitable for diverse manufacturing equipment.
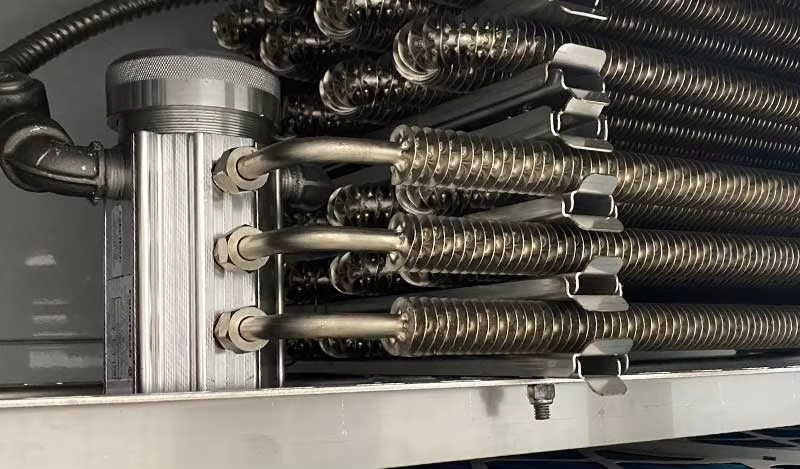
Within the food processing industry, tubular heaters are ubiquitous due to their efficiency and reliability. They are utilized in ovens and grills for consistent baking and grilling, ensuring that food is cooked evenly and thoroughly. In dairies, tubular heaters are applied in pasteurization, where precise heating is necessary to eliminate harmful bacteria without compromising the nutritional value of the milk. Furthermore, in brewing, they help maintain exact temperatures crucial for enzyme activation and yeast fermentation, thereby impacting the quality and flavor of the final product.
Industrial heating systems also leverage the versatility of tubular heaters. They are used in water and air heating systems in various plants and facilities. For example, in power generation plants, tubular heaters are installed in steam boilers to achieve the necessary steam temperature efficiently. In chemical processing plants, they aid in maintaining the right temperature for chemical reactions, contributing to safety and efficacy. Case studies have shown that integrating tubular heaters in such systems leads to significant improvements in efficiency and cost-effectiveness owing to their rapid heat-up times and uniform heat distribution.
These examples illustrate the inherent versatility of tubular heaters, making them a preferred choice across a wide range of applications. Their design flexibility, high efficiency, and durability ensure that they meet the stringent demands of different industries, thereby underscoring their indispensable role in modern industrial and commercial processes.
Advantages of Using Tubular Heaters
Tubular heaters are renowned for their numerous advantages, making them a preferred choice across various applications. One of the primary benefits is their easy installation and maintenance. These heaters require minimal effort to set up, and their straightforward design ensures that maintenance is both manageable and cost-effective. This ease of use is particularly advantageous in industrial settings, where operational efficiency is paramount.
Another notable advantage is the excellent temperature control offered by tubular heaters. They are engineered to provide precise and consistent heat distribution, making them ideal for applications requiring meticulous thermal management. This precision is largely attributed to their uniform heat dispersion capabilities, which ensure that the target area or medium is uniformly heated, thereby optimizing performance.
The construction of tubular heaters from high-quality materials further enhances their appeal. Typically made from stainless steel or other durable metals, these heaters are built to withstand high temperatures and resist corrosion. This robust construction translates into long-lasting performance, reducing the need for frequent replacements and thus contributing to lower maintenance costs over time.
Flexibility in sizes and configurations is another significant advantage of tubular heaters. Manufacturers offer a wide range of options, allowing customers to choose or customize heaters to meet their specific requirements. Whether it’s for small-scale laboratory applications or large industrial processes, the versatility of tubular heaters ensures that they can be tailored to fit any need.
Lastly, energy efficiency is a critical factor that sets tubular heaters apart. These heaters are designed to convert nearly all the electrical energy they consume into heat, ensuring minimal energy wastage. This high efficiency not only helps in reducing operational costs but also supports sustainability goals by minimizing energy consumption and lowering the carbon footprint. Na ovaj način, tubular heaters present a cost-effective and environmentally friendly heating solution for a variety of applications.
Choosing the Right Tubular Heater for Your Needs
Selecting the appropriate tubular heater for your specific application is paramount to achieving optimal performance and longevity. It begins with an assessment of heating requirements. Determine the wattage needed to reach the desired temperature and ensure it aligns with your power source specifications. Understanding the precise thermal demands of your application helps in identifying a tubular heater with the adequate heat output to meet those needs without energy wastage.
Material compatibility is another crucial factor. Tubular heaters come in a variety of materials like stainless steel, Incoloy, or copper, each suited to different applications. For instance, harsh industrial environments may necessitate the use of stainless steel for its corrosion-resistant properties, while processes involving water heating could benefit from copper due to its excellent thermal conductivity. Ensuring the material matches the environment of use not only maximizes efficiency but also extends the service life of the heater.
Environmental considerations cannot be overlooked. Assess the operational environment—this includes factors such as ambient temperature, exposure to corrosive elements, and humidity levels. Opt for tubular heaters designed to withstand the specific conditions they will be exposed to. For example, environments with high moisture levels may require heaters with added moisture-resistant properties.
Customization needs vary across applications. Tubular heaters can be customized in terms of length, watt density, and mounting options. Evaluate whether a standard model will suffice or if custom engineering is needed to tailor the heater to your specifications. Collaboration with a reputable manufacturer can yield bespoke solutions that enhance performance and fit seamlessly within your existing setup.
Installation and maintenance are pivotal to ensuring the effective operation of tubular heaters. Proper installation requires adherence to manufacturer guidelines, ensuring correct fittings and electrical connections. Routine maintenance checks are essential for detecting wear and addressing potential issues before they escalate. Implementing these practices will not only optimize heater performance but also prolong their operational lifespan.
In conclusion, a thorough understanding of heating requirements, material compatibility, environmental considerations, and customization options are essential when choosing the right tubular heater. Attention to proper installation and maintenance ensures not only optimal performance but also enhances the longevity of these versatile and efficient heating solutions.