Understanding the Principle of Heat Tracing Cables
In the world of thermal management, heat tracing cables stand out as a pivotal technology. These cables are essential for maintaining and regulating temperatures in various applications, from industrial processes to residential heating. But what exactly are heat tracing cables, and how do they work? This article delves into the principle of heat tracing cables, breaking down their design, functionality, and applications.
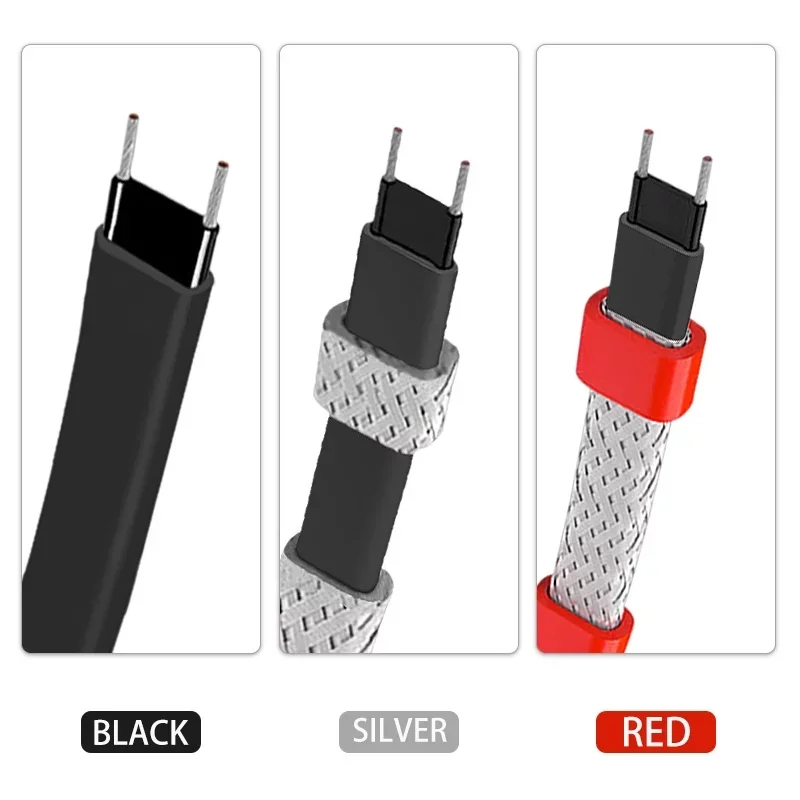
What Are Heat Tracing Cables?
Heat tracing cables, also known as heat trace cables or heating tapes, are specialized cables used to maintain or raise the temperature of pipes and surfaces. They are widely used in industrial, commercial, and residential settings to prevent freezing, maintain process temperatures, and ensure the smooth flow of liquids.
The Core Principle
At the heart of heat tracing cables is the principle of electrical resistance. When an electric current passes through the cable, it encounters resistance, which generates heat. This heat is then transferred to the pipe or surface that the cable is attached to, ensuring that the temperature remains within a desired range.
Types of Heat Tracing Cables
There are two primary types of heat tracing cables: constant wattage and self-regulating.
- Constant Wattage Heat Cables: These cables provide a uniform amount of heat output per unit length, regardless of the surrounding temperature. They are typically used in applications where a consistent level of heating is required. The design includes a resistive wire that runs the length of the cable, encased in insulation and a protective jacket.
- Self-Regulating Heat Cables: These cables adjust their heat output based on the ambient temperature. They contain a semi-conductive polymer core that increases its resistance as the temperature rises, thereby reducing the current flow and heat output. Conversely, as the temperature drops, the resistance decreases, allowing more current to flow and increasing the heat output. This self-regulating feature makes them highly energy-efficient and safe.
Tip | Vlast (W/M 10℃) | Max maintain temp(℃) | Max. exposure temp(℃) | Min. installation temp(℃) | Max. length of single power supply |
Low temperature series | 10,15,25,35 | 65℃±5℃ | 105℃ | -60℃ | 7*0.5 100meters; 19*0.32 120meters. |
Medium temperature series | 35,45,50,60 | 105 ℃ ± 5℃ | 135℃ | -40℃ | 7*0.5 100meters; 19*0.32 120meters |
High temperature series | 35,50,60 | 135 ℃ ± 5℃ | 155℃ | -30℃ | 7*0.5 100meters; 19*0.32 120meters |
How Do Heat Tracing Cables Work?
The working mechanism of heat tracing cables can be better understood by examining their components and design.
- Conductive Core: The core of the cable is made of a conductive material, usually a metal wire or a semi-conductive polymer. This core is responsible for generating heat when an electric current passes through it.
- Insulation Layer: Surrounding the conductive core is an insulation layer that prevents heat loss and protects the core from environmental factors.
- Protective Jacket: The outermost layer, known as the protective jacket, shields the cable from physical damage, moisture, and chemical exposure.
- Termostat (Optional): Some heat tracing systems include a thermostat to provide additional temperature control. The thermostat can turn the cable on or off based on the temperature readings, further enhancing energy efficiency.
Installation and Usage
Heat tracing cables are installed by attaching them directly to the pipes or surfaces that require heating. They can be wrapped around the pipes in a spiral pattern or laid parallel along the length of the pipes. The choice of installation method depends on the specific application and heating requirements.
Applications
They are used in a variety of applications, including:
- Freeze Protection: Preventing pipes from freezing in cold climates.
- Process Temperature Maintenance: Ensuring that industrial processes maintain a consistent temperature.
- Roof and Gutter De-Icing: Preventing the buildup of ice dams and icicles.
- Floor Heating: Providing radiant floor heating in residential and commercial buildings.
Benefits of Heat Tracing Cables
The use of heat tracing cables offers several benefits:
- Energy Efficiency: Self-regulating cables adjust their heat output based on the surrounding temperature, reducing energy consumption.
- Safety: These cables are designed to prevent overheating, reducing the risk of fire hazards.
- Versatility: Heat tracing cables can be used in a wide range of applications, from industrial to residential.
- Reliability: They provide consistent and reliable heating, ensuring that processes and systems operate smoothly.
Conclusion
Kabel za praćenje toplines play a crucial role in temperature management across various industries and applications. By leveraging the principle of electrical resistance, these cables provide efficient, safe, and reliable heating solutions. Whether it’s preventing pipes from freezing or maintaining process temperatures, heat tracing cables are an indispensable tool in modern thermal management.